The Role of Manufacturing on Earth Day
- Susanne Nordman
- Apr 12, 2023
- 2 min read
Updated: May 9, 2024

We’ve all heard the phrase “reduce, reuse, recycle”, but how much thought do we actually put into making changes that will benefit our environment?
Businesses around the world are making changes, both big and small, to contribute to saving our planet. Where does the manufacturing industry come in and what actions can we take to contribute?
Though recycling is a great way to help the environment, reusing material is often missed as a great opportunity to contribute to our planet earth. The European Remanufacturing Network states that keeping components and their embodied material in use for longer periods of time can avoid significant energy use and emissions to air and water (e.g. CO2 and SO2).
Similar to the concept of reusing is remanufacturing. A growing industry, remanufacturers play an important part in sustainability in manufacturing.
Remanufacturing is defined by the Remanufacturing Industries Council as a "comprehensive and rigorous industrial process by which a previously sold, leased, used, worn, remanufactured, or non-functional product or part is returned to a like-new, same-as-when-new, or better-than-when-new condition from both a quality and performance perspective, through a controlled, reproducible, and sustainable process."
Benefits of remanufacturing
Dismantling the product occurs, which means that engineers can guarantee that each part will be tested to ensure original specifications are functioning.
Avoids obsolete parts and machines
Environmentally sustainable, reduces waste
The conservation of raw materials
Increases customer loyalty and satisfaction
Creates jobs in skilled trades
This process is found in many different specific industries, such as aerospace, machinery, and locomotive systems to name a few and is a growing industry itself. Remanufacturing provides over 450,000 jobs worldwide and encompasses a multitude of job function, such as sales, marketing, machinists, engineers, and scientists.

Obsidian Manufacturing Industries, Inc. has helped multiple customers with full OEM rebuilds of their Arter Precision Grinding Machines, returning the machine and parts to like-new.
Not only do we save the material from potentially being scrapped, we save the additional costs that go into the operation of scrap yards and the footprint that manufacturing the replacement machine would have on the environment.
This process also applies to our other products as well. We tend to use the term "repair" when we talk about chucks and lift magnets, but we are remanufacturing each time we perform a full repair on either item.
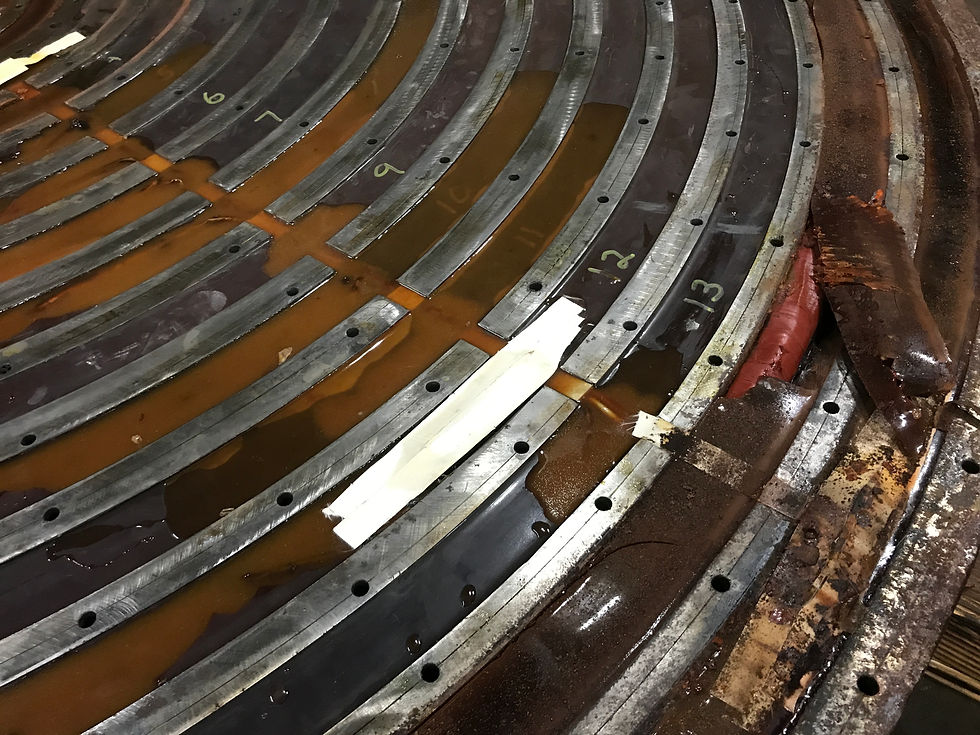
Each magnetic chuck that we repair, we remanufacture the circuit that is providing the magnetic force to hold parts.
By doing this, we are saving a massive amount of energy consumption, reducing waste, and reducing the cost of a new magnet.
Earth Day is celebrated yearly in the month of April, but we challenge businesses to celebrate Earth Day every day and consider our home planet in every action you take as business owners. According to Earth Day organizers, companies who’ve developed strong Environment Social Governance (ESG) standards are seeing better profitability, stronger financial performance, and happier employees. One question remains, what are you waiting for?
This blog was originally written by Rebecca Gomez, former Marketing Assistant at Obsidian Manufacturing Industries, Inc.

Obsidian Manufacturing Industries, Inc. is a Rockford, Ill. manufacturing company and is the OEM for Magna-Lock USA workholding, MagnaLift & Power-Grip lift magnets, and Arter Precision Grinding Machines as well providing surface grinding services. They are located at 5015 28th Ave. in Rockford, Ill. with a phone number of 815-962-8700. Check out more at obsidianmfg.com/brands.
Comments